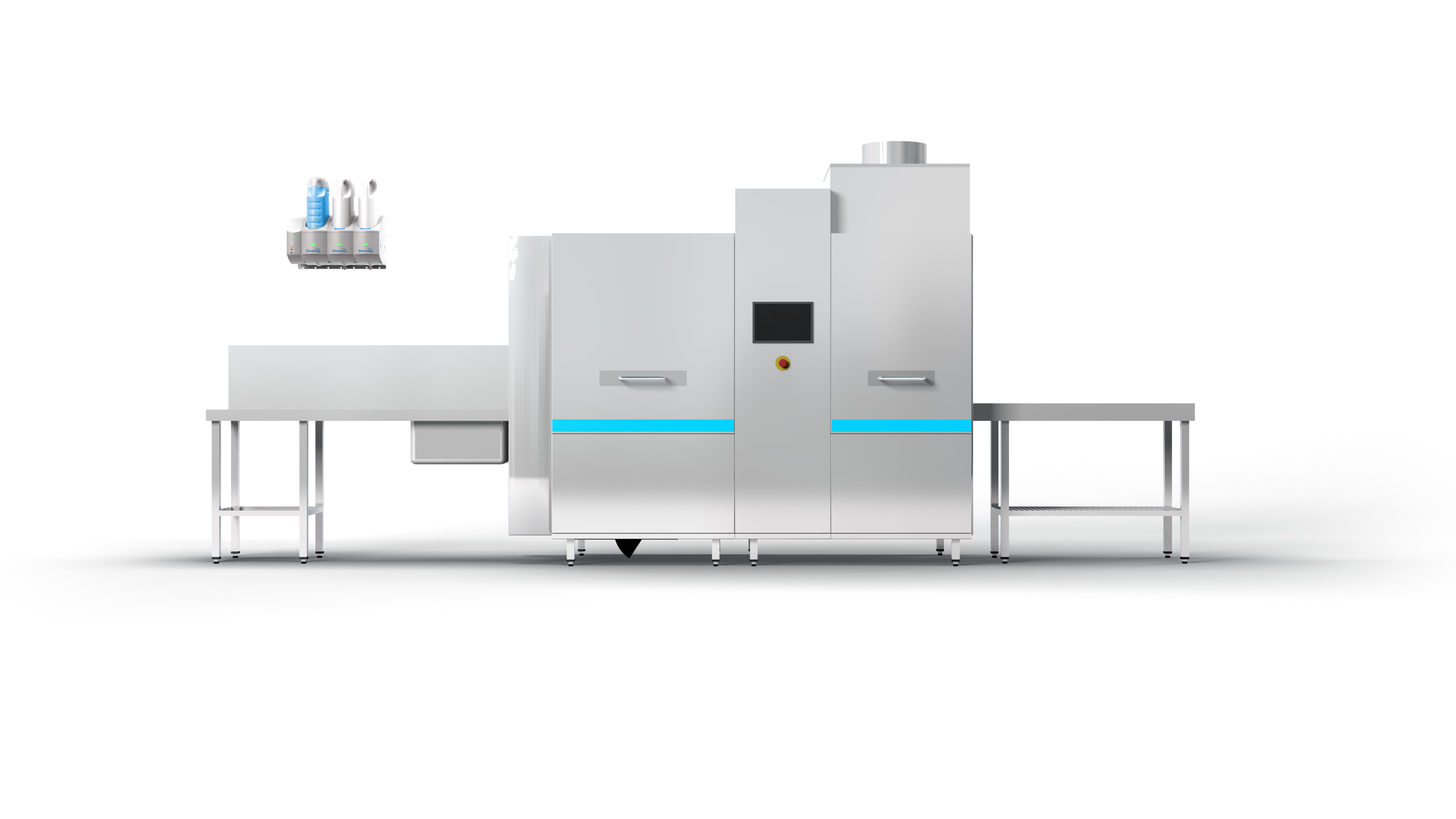
Dishwashing is connected to 60 percent of what happens in a kitchen and has a major impact on operational efficiency. Disruption to dishwashing and poor results cost money and can negatively impact on customers’ experiences, perceptions and satisfaction ratings.
Continuous, efficient and high-performance
The real-time remote diagnostic, reporting and management capabilities of IntelliDish help foodservice operators avoid these pitfalls to maintain continuous, efficient and high-performance kitchen operations. Operators have greater control to improve results and reduce costs while maintaining food hygiene and safety compliance.
IntelliDish acts as an analyst across all the operator’s kitchens to monitor performance continuously and ensure systems are running optimally, efficiently and profitably. It utilises advanced ‘smart’ technology to track and report accurate dishwashing information. Working in conjunction with Diversey’s Revoflow dispensing system it communicates various aspects of a dishwashing machine’s cycle (including pre-wash, wash, and rinse temperatures, product usage and concentrations) to a cloud-based server.
Information is automatically and instantaneously analysed so that status reports and alarms are shown immediately on an interactive user dashboard. This provides a clear and intuitive view of what is happening in every connected dishwashing machine. The system also sends alerts to authorised email recipients to enable rapid response. This includes, for example, when energy, water or detergent usage exceeds predetermined limits. Information required to resolve issues is provided in the form of video attachments and contextual content that also acts as training material.
Key efficiency metrics
A critical requirement for many operators is to reduce rewash rates, a key efficiency metric with industry averages running at around 10 percent. High rewash rates are often attributed to non-optimised processes that also increase per-rack costs. Estimates also suggest between two and three percent of dishwashing costs in food service and hospitality result from breakages, when kitchens are forced to wash dishes manually or have a high rewash rate that requires more handling (increasing likelihood of breakages).
The status updates and dynamic training enabled by IntelliDish help maximise machine uptime and “right-first-time” washing to avoid these and other issues.
With IntelliDish, operators can prepare detailed reports and make more informed business decisions, anytime and anywhere. They can identify consistent pain points that are reducing profitability and prevent them re-occurring by taking immediate corrective action, thereby supporting predictive and proactive maintenance strategies to maximise machine availability. By ensuring processes are less labour-intensive the system helps kitchen staff make the best possible use of their working hours.
Live sites have demonstrated that savings enabled by IntelliDish quickly return the investment in the service. Data collected and stored by the system provides a detailed audit of operations for simpler food safety and hygiene compliance reporting.
Further details:
IntelliDish is designed as part of Diversey’s Internet of Clean platform, which includes a variety of connected technology solutions for commercial cleaning – providing full visibility of operations to improve efficiencies and reduce costs.
Further information in the UK on 0800 525525 or http://www.diversey.com
Further information in Ireland on 01 808 1808 or http://www.diversey.com
Diversey is a leading hygiene and cleaning solutions company that integrates chemicals, floor care machines, tools and equipment, with a wide range of technology-based value-added services, food safety services and water and energy management. Diversey employs approximately 8,600 people globally and generated net sales of approximately $2.6 billion in 2016. For more information, visit www.diversey.com.